Endmatched Flooring
Of all the steps involved in making flooring, endmatching the boards has been the hardest for us to achieve. It requires a very specialized machine and a high degree of precision. While ubiquitous with the big flooring producers, endmatching is not a requirement for narrow flooring under 5” in width. Because of the hurdles involved, I have gotten by without offering an endmatched floor. I stuck to only making narrow flooring, providing a very accurate square end trim, and working with highly-skilled installers who know their way around non-endmatched flooring. As a result, the quality of a Zena Floor was never compromised, but endmatching has been on my to-do list for over a decade. It adds a measure of convenience for the installer, it opens the door to wider flooring, and ensures an added level of stability for the floor.
I should take a moment to explain what endmatching is. Hardwood flooring usually has a tongue and groove running along the sides of the board, called a side-match. An end-match is a tongue and groove profile on the ends of the boards. This helps to hold everything flat and creates a fully interlocking floor. It sounds simple, but my quest to find a way to mill this in a production environment has been a long, arduous and expensive saga.
After years of looking and learning about end-matching machines, I came to the conclusion that only one company ever built a machine that will fit our application. And… the company went out of business in 2003. This machine also has a computer in it. I like to work on all of the machines here myself, but PLC’s and the like are way over my head. So with no customer support and specialized electronics, I knew I was in for a challenge. Luckily there are a number of these machines on the used market, so in July of 2016, I took the plunge and purchased an Auburn Endmatcher from Minnesota. It was working when I received it, but in the time it took us to rebuild our flooring line in preparation for endmatching, something went haywire with the machine and it refused to cooperate.
Thankfully my friends at Wurdinger Manufacturing came to the rescue. I placed the machine in their capable hands, and slowly and methodically they went through the machine with a fine-tooth comb. After many attempts to resurrect the brains of this machine, we ended up installing a new computer and completely reprogramming the machine from the ground up. Finally, after lots of setup trial and error and an enormous number of hours spent with this machine, I have a working endmatcher.
When we ran our first batch of flooring through this machine, the guys patiently put up with me as I ran back and forth looking over shoulders and inspecting the machine and flooring ends equipped with a square and caliper. Needless to say I had a smile plastered on my face all day. Our new machine cranked out tight, perfectly flat and square joints all day long.
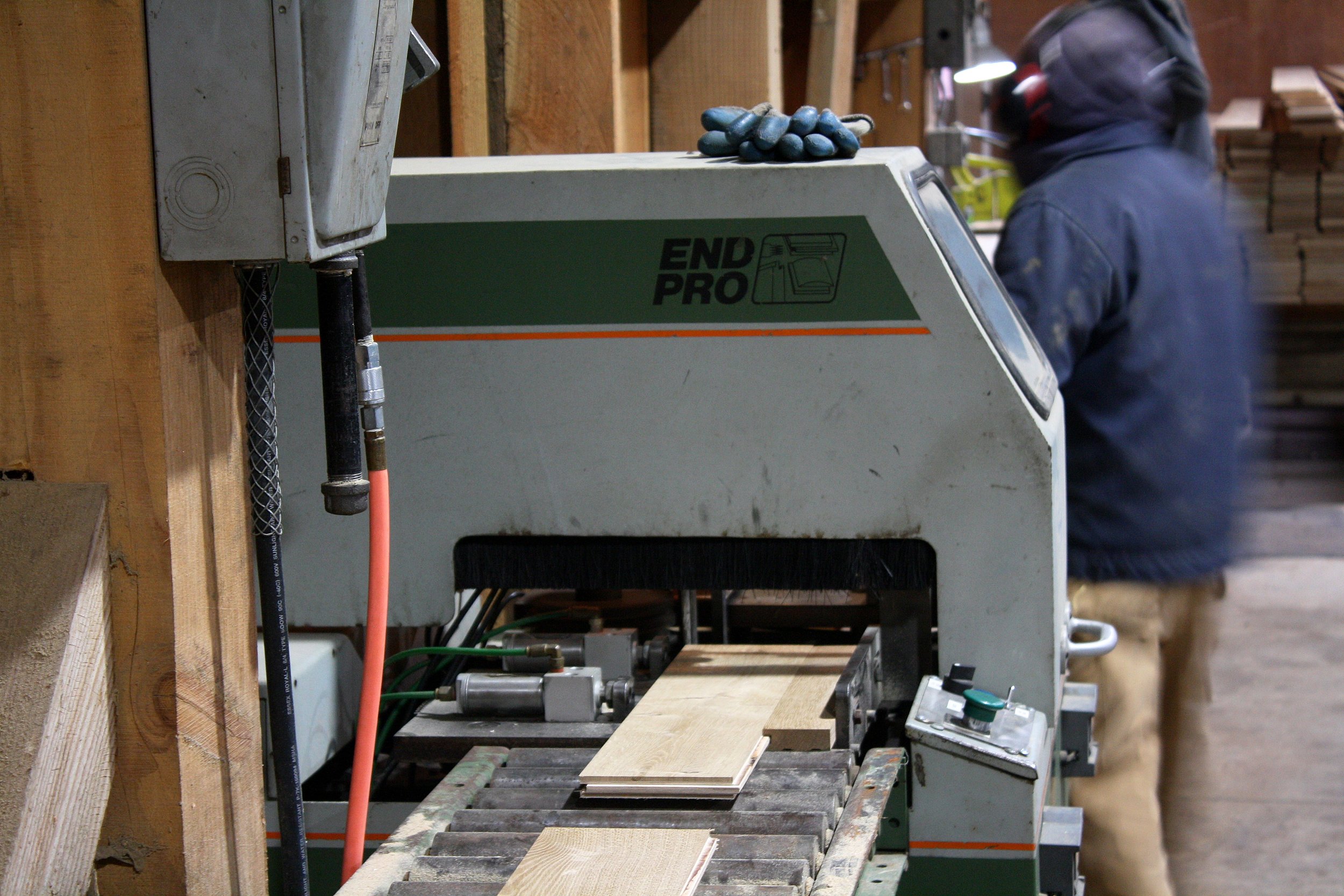
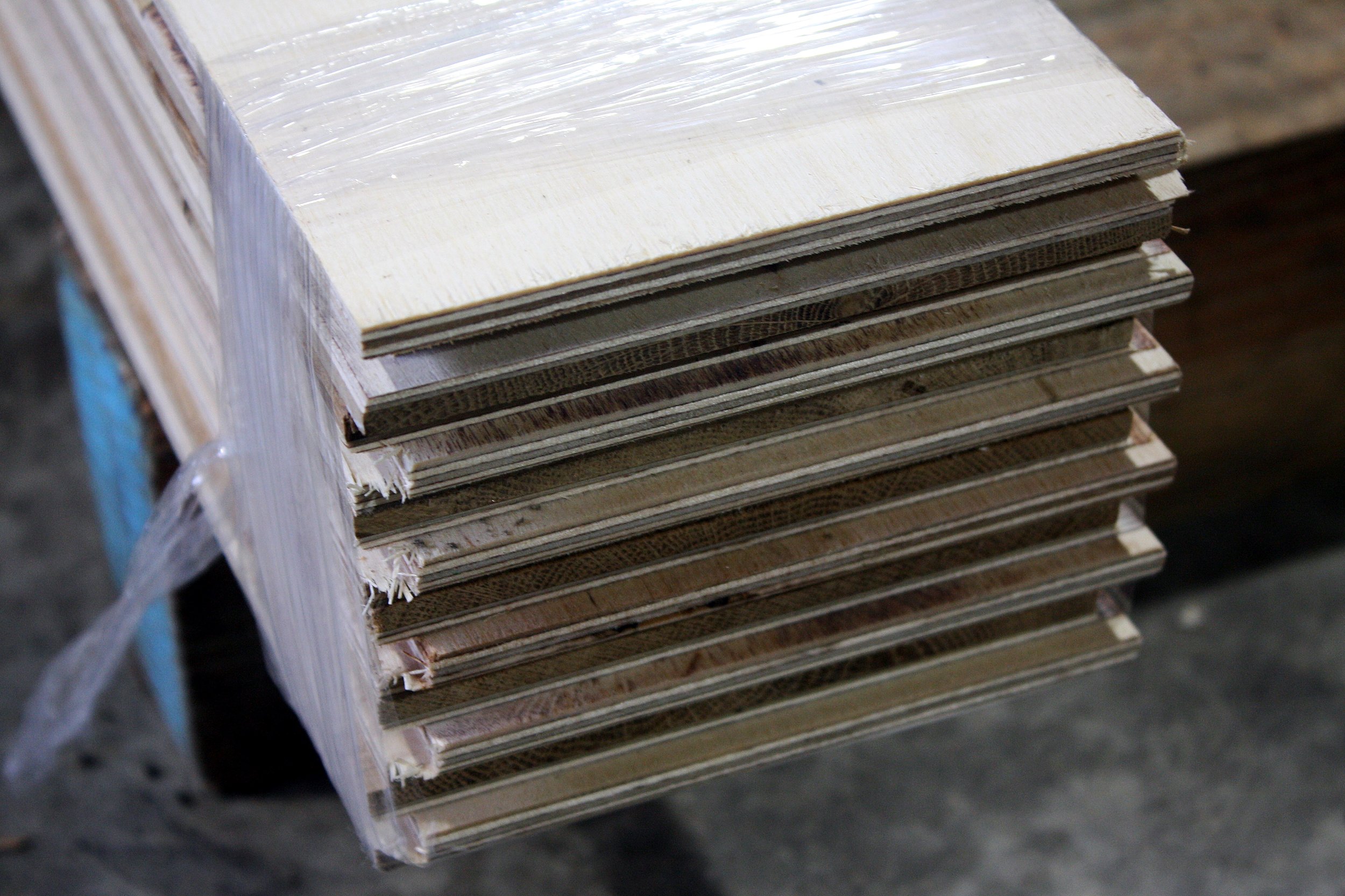
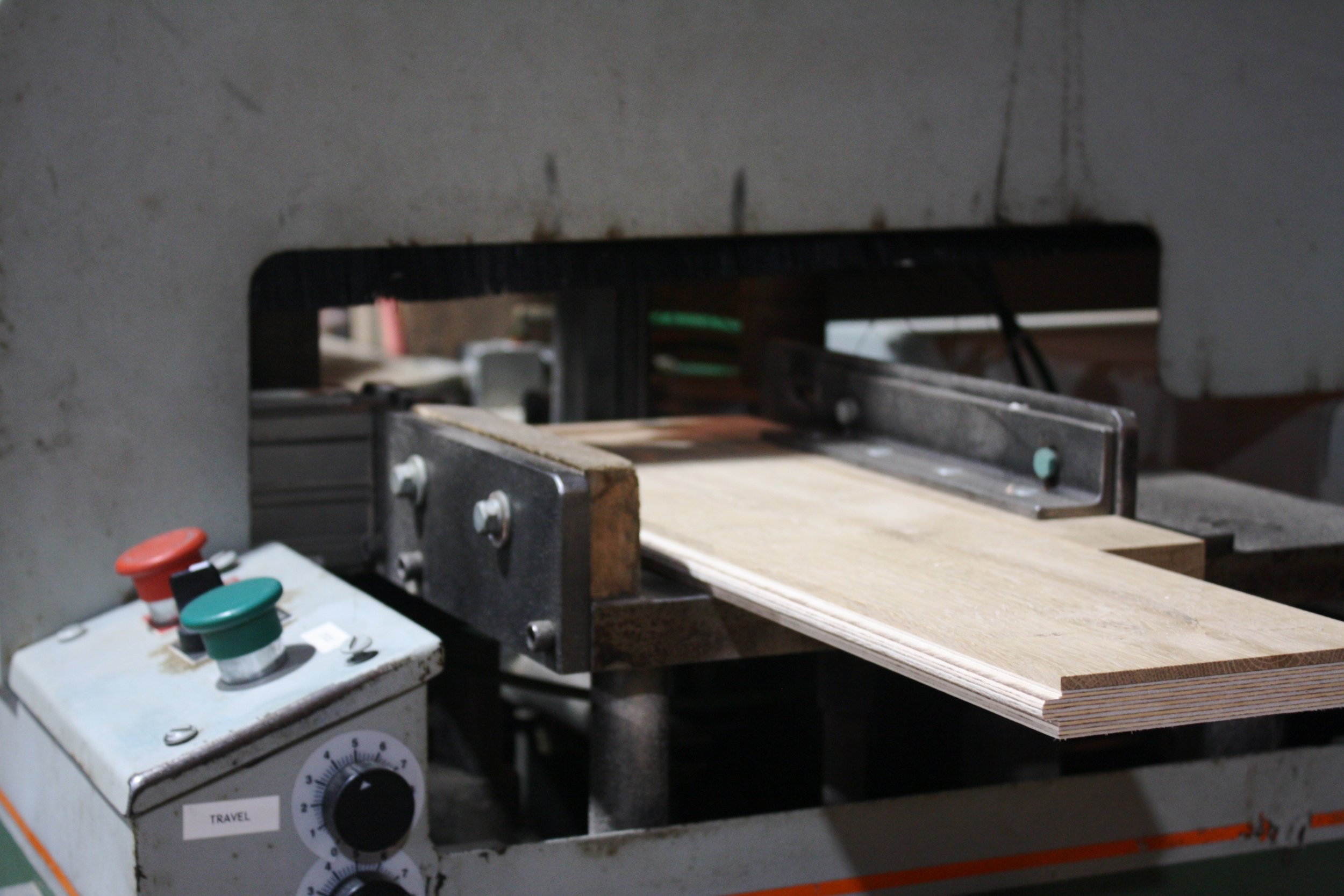
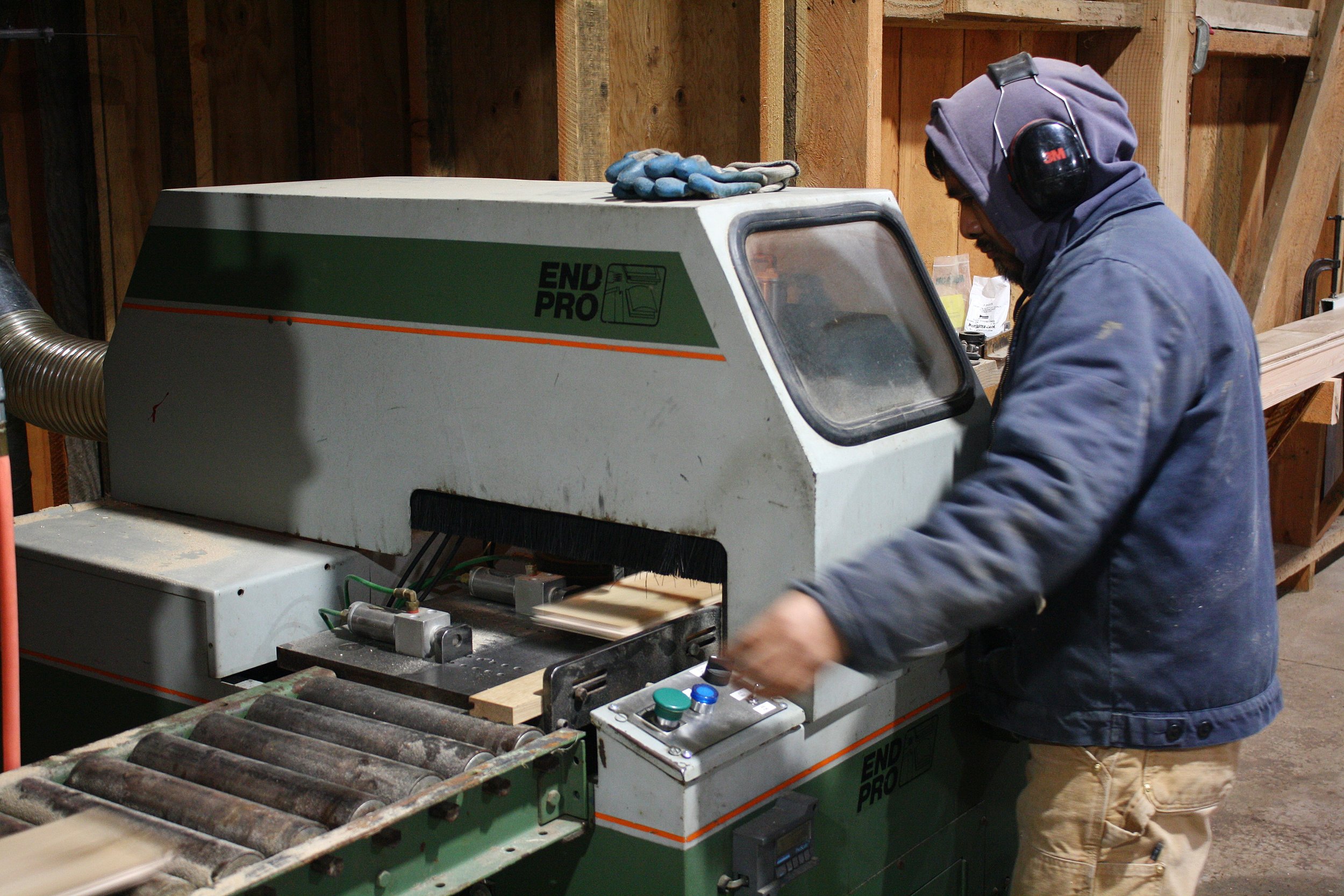